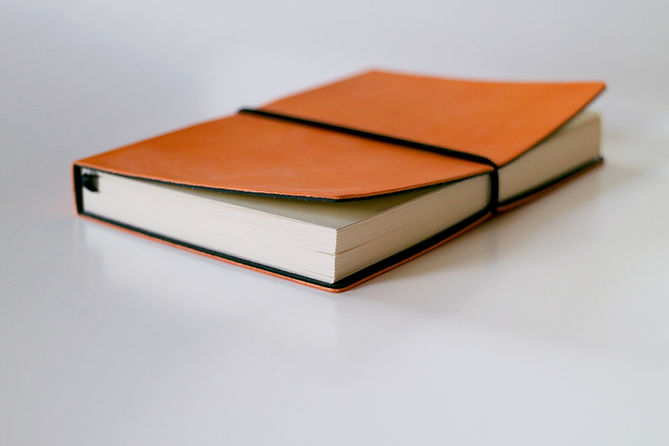
Site Articles
The main purpose of this page is to give interested parties easy access to some of our more recent articles related to quality systems, implementation, etc. The information provided on this website is not intended to constitute consulting advice; instead, all information, content, and materials available on this site are for general informational purposes only.
05/15/2023
Unlocking the Hidden Potential: How QMS Audit Programs Can Add Value to Your Organization
Whitepaper by: Scott Hackler

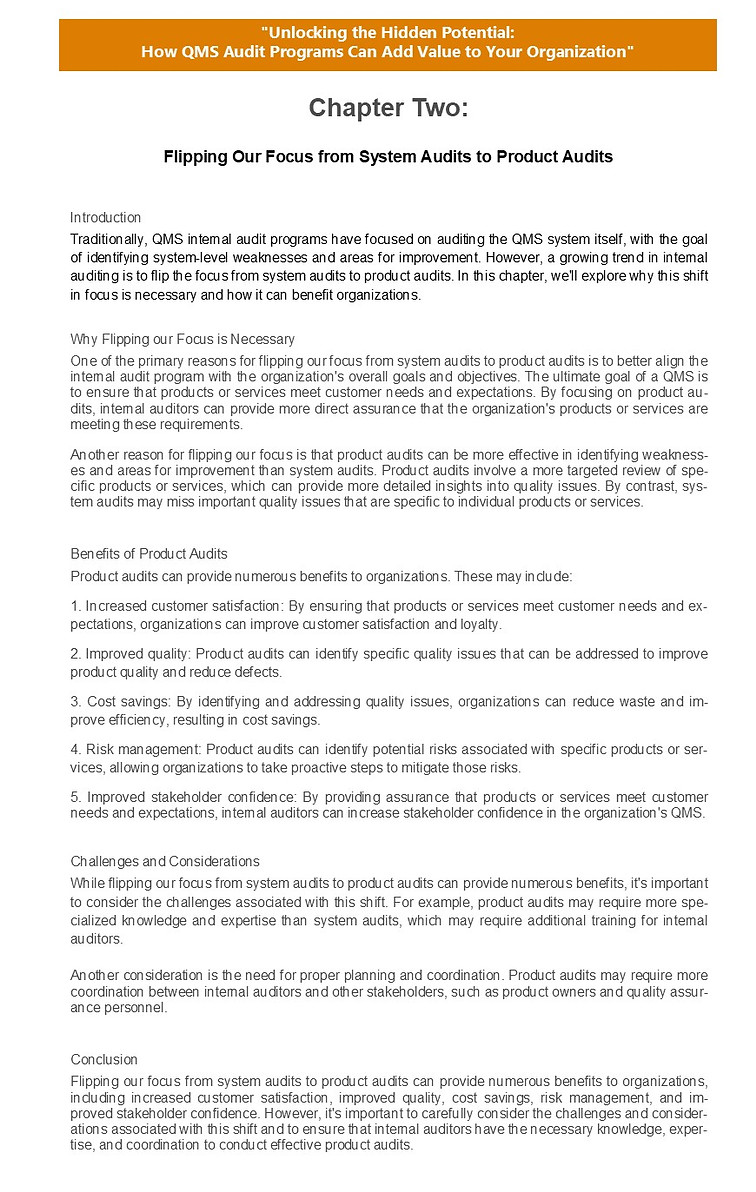


12/13/22
Quality Re-Imagined
To make a great product, you need great processes. When you understand the capability of your systems and processes, you can optimize their quality and performance. Many companies separate their Quality Management System (QMS) from Lean, Six Sigma and other business tools. While implementing or optimizing your quality system, we integrate operational excellence tools, so they work with your QMS.
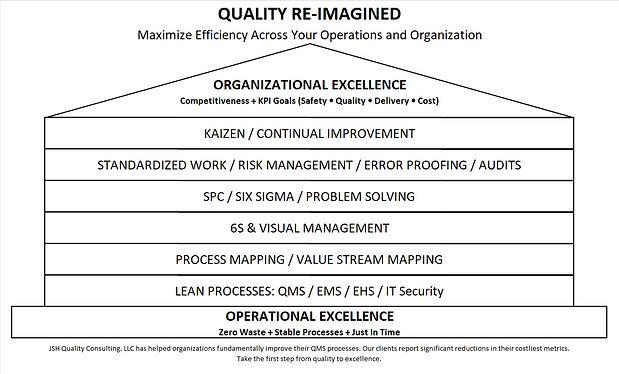
Lean, Six Sigma and other valuable business tools do not provide guidance for integration with an organizations QMS and historically are implemented as stand-alone initiatives. In addition, many organizations tackle QMS, EMS, and OHS standards individually and do not take advantage of the synergy that was designed into these standards. Most companies focus on compliance or certification as the primary objective, instead of value. Continual quality and process improvement tools (e.g. Lean and Six Sigma) are almost never included. The logical conclusion is JSH Quality Consulting's approach to integrate these quality and improvement tools with a QMS. Thereby efficiently, practically, and rationally developing the Operational Excellence that is a true foundation for continual improvement and Organizational Excellence.
​
The true value of a QMS can only be grasped if organizations set in place effective processes that lead to improvements in quality within the organization. In addition, business improvement processes should be part of a continually improving quality management system. Integrating quality and improvement tools (i.e. Six Sigma) with a QMS helps organizations in assuring that there is no regression to the old processes after Six Sigma implementation. Organizations benefiting from Six Sigma often forget the importance of building a quality system, which is crucial to continually improve the quality while decreasing nonconformities. Both QMS and Six Sigma complement each other perfectly to achieve even more sustained results as opposed to being implemented separately.
Scott Hackler

08/20/2022
Maintaining Certification
Many businesses err in thinking a Quality Management System (QMS) is a static entity. It isn't. A QMS needs to evolve in order to reflect your company's evolution; it must be allowed to develop as market conditions change and your products and technologies improve, and; evolve as your interested parties grow and their needs expand. By treating your QMS as a living entity, the more likely your company will realize quantifiable benefits and maintain certification.
​
​
I have seen many companies put all their efforts and resources into the implementation of their QMS only to obtain certification. After which, the QMS is only "caught-up" just weeks prior to their upcoming surveillance audit. If you have to catch up or prepare your system for an upcoming surveillance audit, you know for sure your QMS is dead.
​
I believe internal auditing is the key to keeping your QMS alive. For most companies, an internal lead auditor is someone that has multiple responsibilities within the organization. I get that. However, we are talking about a quality system that is integrated with the organization's business system and just like any other aspect of your business system, require a high priority.
Internal audits shouldn't just be a check on a to do list. We must see internal audit as a continuous improvement tool whose sole purpose is to improve the performance of all processes of the organization. The audit is designed to add value and improve the operations of a particular organization. If ample focus is placed on internal auditing and it is performed a few times each year, it can be the best way to keep up on the requirements that you implemented to improve your organization from the beginning. The character of an internal audit is to inform the governing bodies of an organization about the risk factors and operational effectiveness. The ultimate goal of an internal audit is to recognize weaknesses within the organization so that they can be fixed quickly to prevent the organization from further harm.
Take stock in the internal audit process. By evaluating the company's policies and procedures, one can make sure that they are doing what the company policies say, and that these procedures are satisfactory in making your business risks less severe. Internal auditing is good because it helps in the betterment of the environment of the organization by evaluating the efficiency and utilizing the effectiveness.
​
If you invest in internal auditing, there will never be a need to "prepare" for your upcoming surveillance audit.
Scott Hackler
03/17/2022
Template Kits
We are often asked about the use of ISO pre-written templates used for documentation requirements. ISO templates have been around since the first version of the Standard was published in 1987. I myself have used templates when I started out implementing my first QS-9001 standard. I’m not a big fan of the use of templates, however, if you know going into it that these templates are generic and need to be adapted to the organization's situation, then using them as a guide can be beneficial. If the templates are designed correctly, their intent is to meet the basic standard requirements but it’s important that you not rely on the template as written.

I have audited companies that used templates, and, at times, it was obvious that they were templates – they were very generic and did not describe the specific activities that were actually taking place. Templates are useless as ISO documentation unless they are carefully customized to meet the very specifics of your organization. Good customization is necessary to adapt the template to the organization's individual situation.
​
Many people like using templates simply because they need a place to start, and they want that reassurance that they are on the right track – we get it! Because of their obvious growing popularity, many of our clients have come to expect the use of templates as part of a consultant’s service. My company does offer templates for this reason; however, we also like to be there for the restructure of the template to ensure its added value to your system.
​
There are many ISO template options out there. I’m even aware of a fellow- consultant providing templates online for free, stating “template kits suck, but free template kits suck less.” Because the qualitative differences vary widely, it’s obviously important to choose a template kit with the quality and features that work best for you, knowing full-well they will need substantial customization.
​
Scott Hackler

03/10/2022
ISO in a Can
Most recently, our customers are companies that have had ISO 9001, IATF 16949 or ISO 14001 certification for some time. What most of these customers have in common is that they originally approached Quality Management System (QMS) implementation and certification from a compliance perspective. Consequently, their QMS was treated as an expense and the requirements as a chore.
Now, they discover that they wasted their resources and missed out on the potential benefits of a well-engineered QMS. Unfortunately, a high percentage of these companies used consultants to help them implement their systems. Don’t let a bad consultant come in with “ISO-in-a-can” and whip-up a QMS. If you're looking to "just get certified," that's generally all your ISO system will be - an expense.
Bad consultants will make money off their customers, good consultants make money for their customers. Make them money and save them money - your reputation is entirely up to you!
​
Scott Hackler